An interactive tool
to train Airbus employees
The Onet University teams have designed an innovative, interactive induction course for all new Onet employees at Airbus.
The objective?
Explain, through tutorials, visuals and videos, all the particularities of the assembly line environment (FAL: Final Assembly Line) and deliver safety rules.
- - Onet
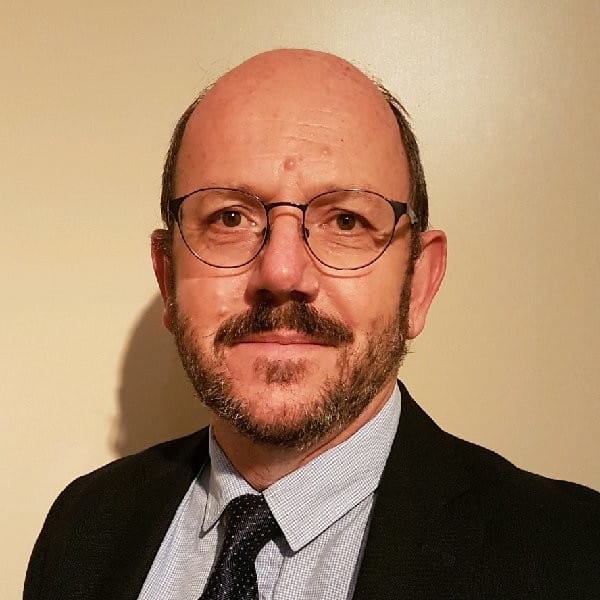
"Maintenance work on Airbus FALs is a very special and demanding task, and our employees must absolutely master the safety and quality rules specific to this working environment before they can start," explains Gilles Boursin, manager of the Toulouse branch.
Because training new Onet employees at Airbus is a major issue, he welcomes the new induction course available on Campus, Onet's online training catalog.
"Previously, we used to train teams with paper-based materials, but this interactive tool enables us to energize the integration process and maintain attention," he explains.
"Thanks to this tool, our employees retain information better. As for the final quiz, it allows us to check their knowledge in a fun way.
A field approach
The result of an excellent collaboration between the Toulouse teams and those of Onet University, this integration program involved immersion at Airbus.
"It was by visiting Airbus sites that we were able to appreciate this very special environment and the repercussions on our employees' working conditions," confides Martine Baronian, head of Onet University.
She adds: "This interactive module enables employees to integrate all the site's particularities and obtain the information they need to ensure optimum safety."
On the menu:
- reminder about Onet,
- lexicon and knowledge of aeronautics and Airbus,
- practical information on Airbus FALs,
- traffic rules,
- anomaly escalation process,
- FOD quality and management - foreign bodies likely to cause damage -,
- waste sorting
- and health and safety rules.
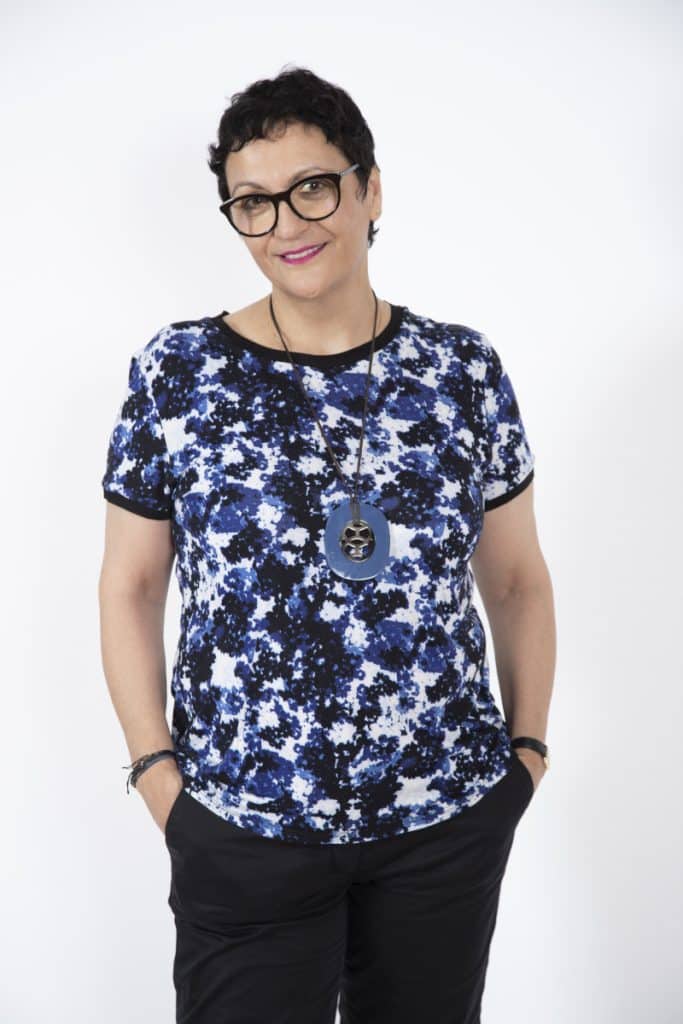
Safety is a top priority
This interactive welcome booklet dedicated to Airbus represents the expertise of Onet's university team.
"We design tailor-made training materials for our customers, based on the reality of their environment, and focusing on the Group's top priority: safety", Martine Baronian sums up. She adds: "We're also there to develop the modules, in line with changes at our customers' sites or regulatory developments." A real asset for field teams, who appreciate the attentiveness of head office.
"Our training programs are bearing fruit: when our employees arrive at an FAL, they are perfectly familiar with the environment, and the feedback from our customers is very good," confides Gilles Boursin, who concludes: "like the quality of supervision, integration helps to reduce the frequency and severity of accidents on site.