Home / Join us / Operational / Ultrasonic non-destructive testing technician - Job sheet
Ultrasonic non-destructive testing (NDT) technician
What is the role of a non-destructive testing technician? What are their missions? What skills are required? Find all the answers to these questions in this job description designed exclusively for ultrasonic non-destructive testing (NDT) technicians!
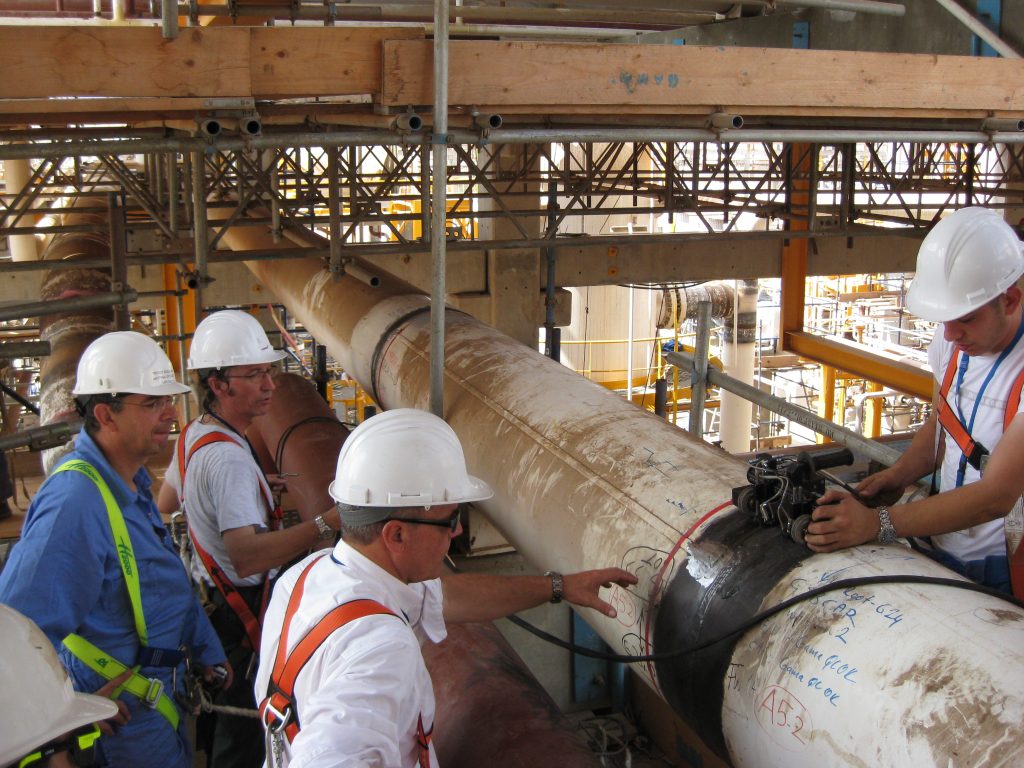
What is the role of an ultrasonic non-destructive testing (NDT) technician?
The job of a non-destructive testing (NDT ) technician involves checking the integrity and conformity of materials or structures without altering them. This includes the use of specific techniques such as ultrasound to detect any cracks, defects or anomalies invisible to the naked eye. With COFREND Ultrasound level 2 certification, the non-destructive testing technician is able to interpret complex results while complying with safety and quality standards. As a non-destructive testing technician, I play an essential role in the prevention of failures and the safety of installations.
My duties and responsibilities
as an Ultrasonic Non-Destructive Testing (NDT) Technician
I carry out ultrasonic quality control of welds on metal parts and assemblies.
I can analyze internal weld defects
I am able to interpret the results and draw up NDT inspection reports for each operation carried out.
I report on my activity.
My challenge is to ensure the conformity of welds at our customers' sites and to guarantee our reliability in the field.
My core competencies
Know-how
Draw up technical documents such as service reports.
Work on the sites of our customers, major players in the nuclear and industrial sectors in France, on long-term assignments.
Working in a constrained environment, respecting safety and security rules and procedures.
Valid COFREND CIFM UT2 certification
Ideally, you should have a BAC +2 in a technical field
A valid B driver's license
Know-how
Adaptable
Rigorous
Respectful of procedures
Vigilant
Team spirit
My manager's vision by Onet
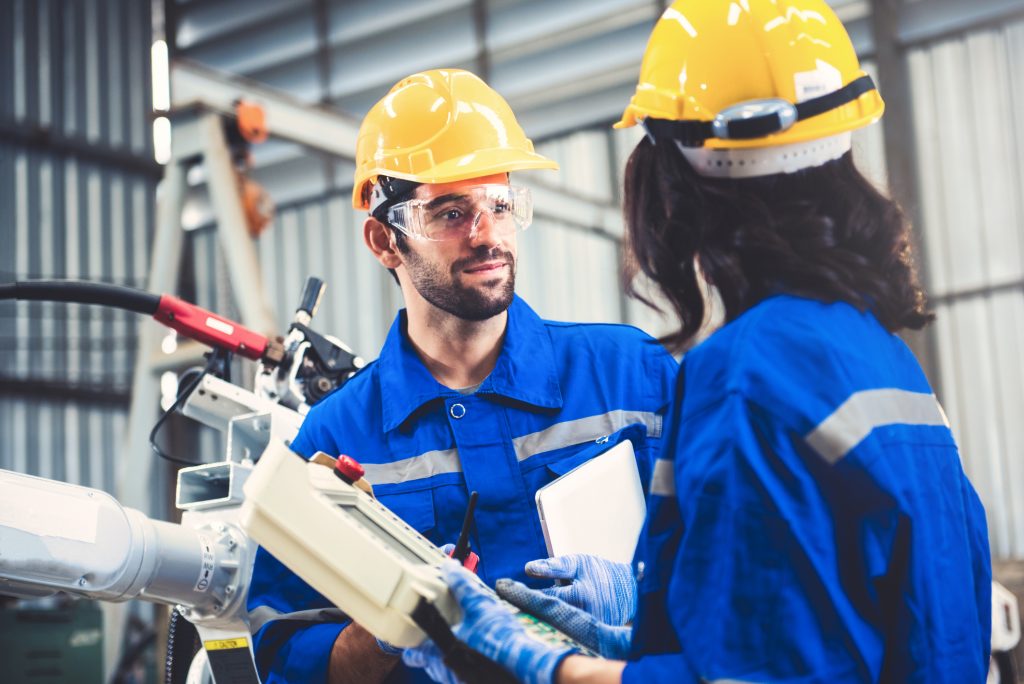
The advantages of my job
Diversity of teams: I work in the field with expert teams
Travel : I travel all over France
State-of-the-art equipment : I use state-of-the-art equipment and tools.
How do I become an ultrasonic non-destructive testing (NDT) technician?
To meet regulatory requirements, control officers must take one of the following training courses.
What training courses are available to become a non-destructive testing (NDT) technician?
- BAC :
- Bac Professionnel Industrial Boilermaking Technician
- Bac Professionnel Industrial Boilermaking Technician
- BTS :
- BTS in Industrial Boilermaking Design and Production
- BTS Design and Industrialization in Shipbuilding
- BTS Foundry
- BTS Metallurgy
- BUT Mesures Physiques
These different educational paths will introduce you to the profession of non-destructive testing technician. You will then need to pass the COFREND certification (French confederation for non-destructive testing) to be able to work as a non-destructive testing technician. This certification, for non-destructive testing (NDT), can be obtained from Onet once you have been recruited.
My career prospects
Be trained in new NDT techniques,
Evolving in the Intervention sector
Managing teams.
What are the different types of non-destructive testing techniques ? ?
The profession of non-destructive testing (NDT) technician relies on a number of specialized techniques to guarantee the quality and conformity of metallurgical products, metal parts and industrial installations. These techniques are used in a wide range of sectors, including the nuclear, shipbuilding, aeronautics and oil industries. Here's an overview of the main NDT methods:
This method uses ultrasonic waves to detect internal defects in materials. The waves are sent into the part, and the echoes are analyzed to identify anomalies such as cracks or inclusions. Ultrasonic testing is essential for the inspection of critical parts in industry, particularly by inspection officers and specialized test technicians.
This technique is mainly used to detect surface defects in conductive materials such as metals. Eddy currents induce magnetic fields that enable discontinuities in the surface of parts to be identified, which is crucial for compliance with quality and safety regulations in industrial processes.
Radiography uses X-rays or gamma rays to inspect the interior of structures without damaging them. Control technicians and plant inspectors rely on this method to examine welds and metal parts, while complying with preventive measures and regulatory safety requirements, particularly with regard to the use of ionizing radiation sources.
This technique relies on magnetizing the part to be inspected, in order to detect defects on the surface or just below. Magnetic particle inspection is particularly effective on steel parts and other ferromagnetic materials, and is often used by professional inspection technicians in the manufacturing and maintenance stages.
A simple and highly effective method, penetrant testing involves applying a penetrating liquid to the surface of the part, followed by a developer, to detect open defects on the surface. This technique is widely used by maintenance companies to check parts subject to high stress.
With the constant evolution of technology, new methods such as infrared thermography and industrial tomography are gaining in popularity. These specific techniques enable even more precise, real-time controls, particularly in industrial quality control contexts where production management demands rigor and continuous adaptation.
These various NDT methods are essential for ensuring the conformity of industrial applications and compliance with safety regulations.
I'm applying!
Jobs - Ultrasonic non-destructive testing technician